
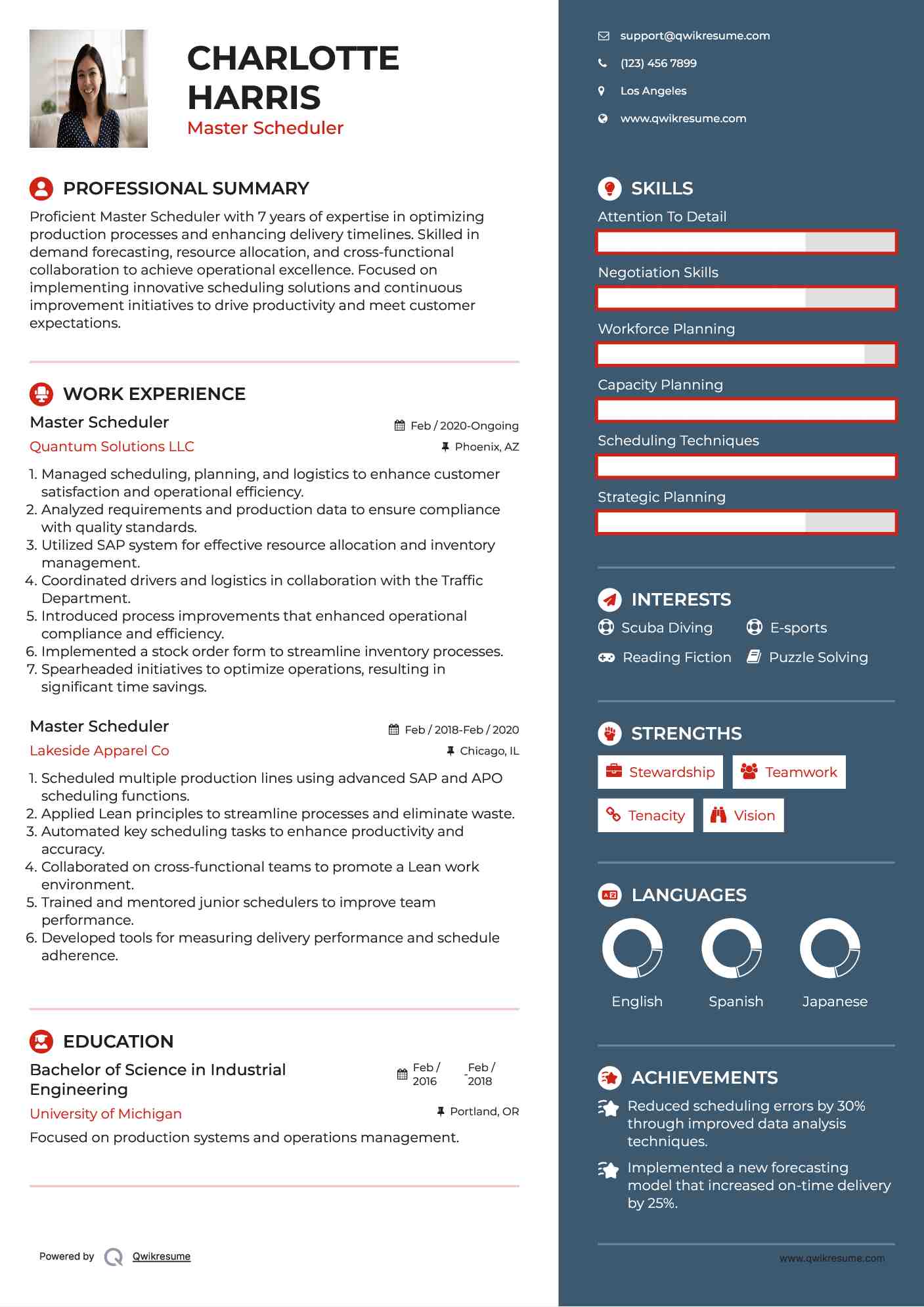
They are usually responsible for balancing demand & capacities and communicating with Master Schedulers, plant supervisors & managers, new product development teams, purchasing, distribution and demand managers to resolve any issues effecting the planning, timing and execution of production for their respective areas. Many times, the production planners are organized into functional areas based on plant locations, work-centers, products manufactured and/or business segments. Planned orders will automatically change with demand signals but firm MPS planned orders, firm purchase orders and live work orders for production will not automatically change which is why the exception reports are critical for identifying the changes that need to be made. Exception reports can be generated anytime and will ‘flag’ firm purchase orders, firm MPS planned orders and live work orders for production that need to be rescheduled or cancelled. This is achieved by monitoring ‘exception’ reports generated by the MRP system. They then work between Supply Chain, Procurement and Demand Management to ensure correct signals are being transmitted back into the MRP and are responsible for effectively communicating gaps between demand and supply as it relates to manufacturing and procurement capabilities. Members of the production planning team work closely and collaboratively with the Master Schedulers to balance workloads across multiple work-center groups and manufacturing plants to ensure all resources are optimally loaded into the MPS module. Additionally, these replenishment signals can change based on inventory adjustments, new or cancelled sales orders, shorted or missed production quantities, changes to system settings and a variety of other reasons. Production planning is based on the demand signals received from the annual constrained forecast that are translated into supply or replenishment signals based on available inventory, lead-time and capacity. There are pro’s & con’s to both approaches depending on the agility of your supply chain and the structure of your planning team.

Other organizations might choose to firm up further into the future and even the entire year. Some organizations only ‘firm up’ production plans inside the cumulative lead-time window and allow planned orders to ‘float’ beyond that window based on demand signals received. Rough cut capacity planning tools understand this complexity so that when you are scenario planning, based on the mix of products you load into the MPS, it optimizes the capacity utilization accordingly. So if half the day is spent on product ‘A’ and the other half day is spent on product ‘B’ then the total production on that resource for the day is 500 units. So for example, product ‘A’ might have an ADR of 600 while product ‘B’ might have an ADR of 400 yet they both are manufactured on the same resource. Usually these calculations are presented in time buckets such as Average Daily Rates (ADR) or how many units, on average can be made per day.Īverages are used because the complexity of each product manufactured on a given resource usually varies. Capacity modeling is basically a mathematical analysis of how many units can be manufactured over a set time period utilizing a specific work-center(s) or resource(s).
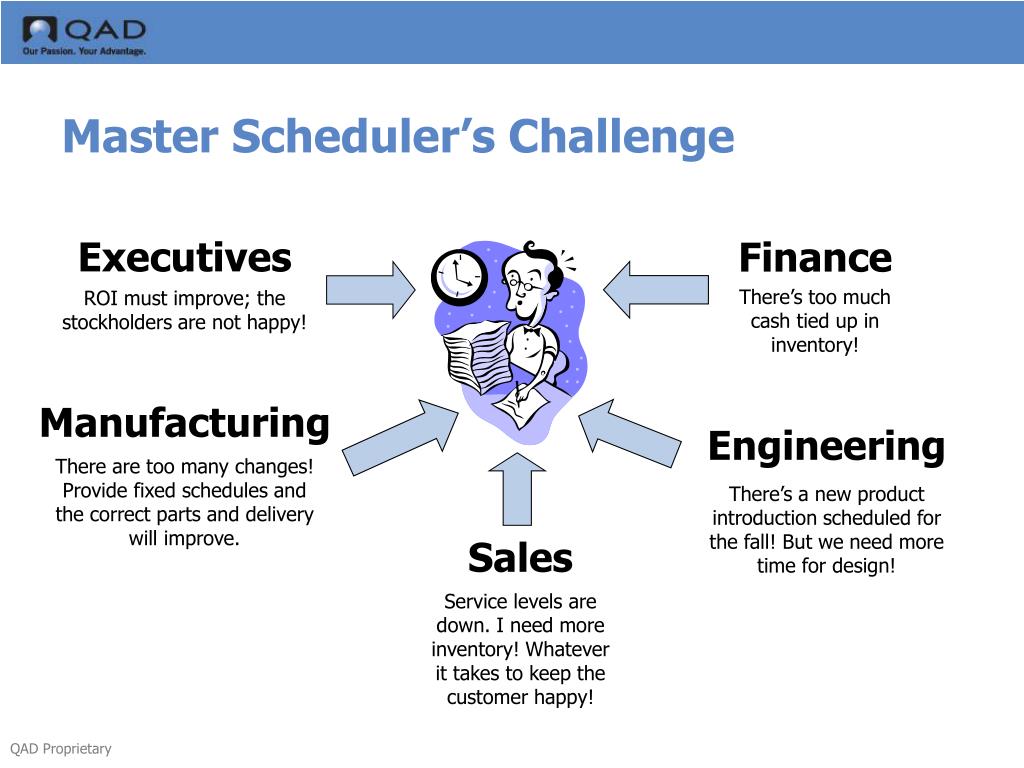
Production planning is the process of modeling the available capacity in order to effectively balance workloads across the organization while keeping in sync with the changing demand picture.
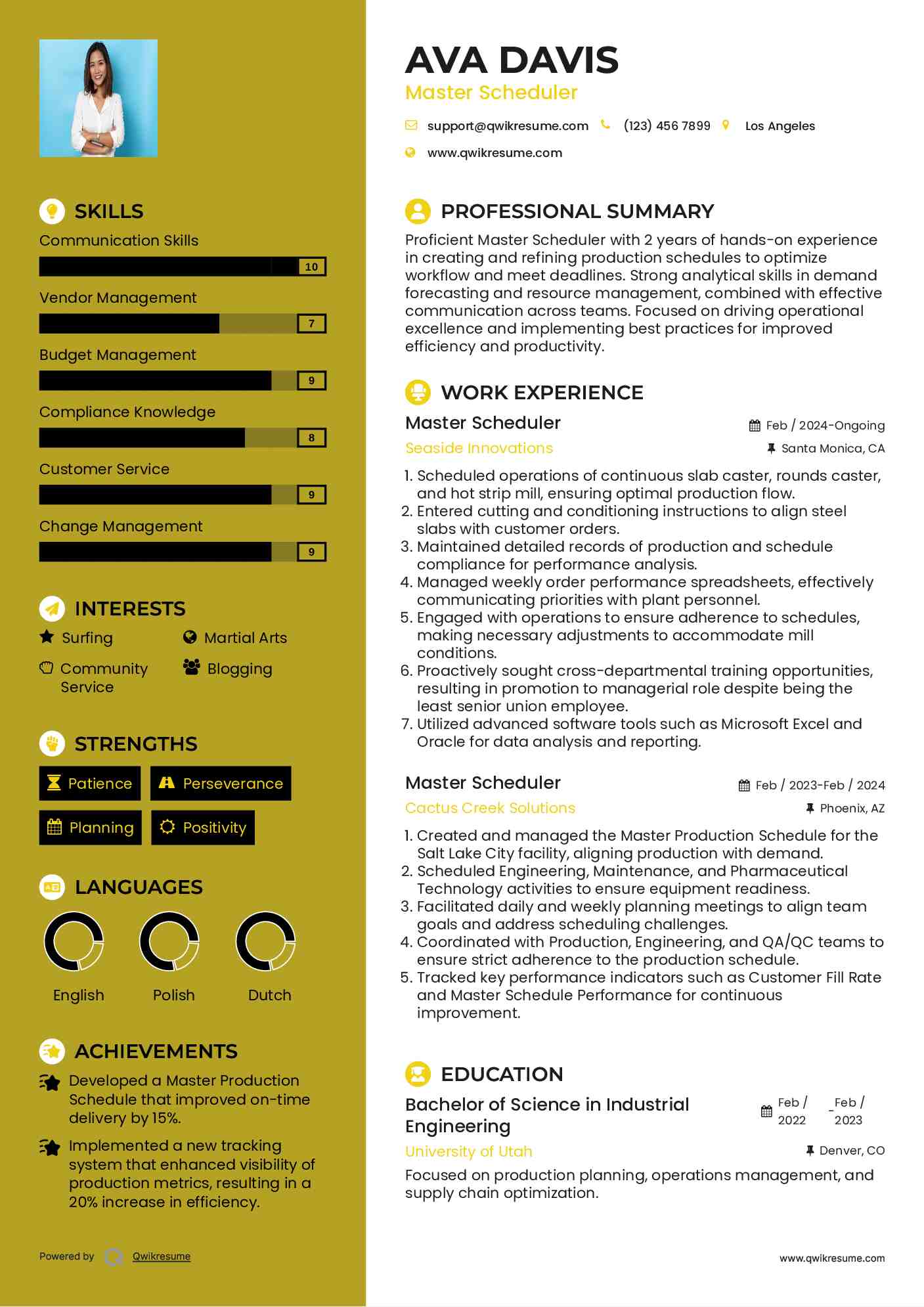
Production planning is critical because you want the plan to be synced to demand, balanced across correct work centers and materially supported as it enters into the scheduling phase of the planning horizon. You can see the problem as any changes made by the master scheduler within the cumulative lead-time window can impact execution activities and create knee-jerk throughout the supply chain. The main difference is that production planning works with MRP planned orders & MPS firm planned orders outside of the cumulative lead-time window while master schedulers work with converting the MRP planned orders into MPS firm planned orders and ultimately into work orders once they come into the execution window or inside the cumulative lead-time. Production Planning and Master Scheduling are sometimes combined depending on the company and their available resources but they have very distinct and differing responsibilities.
